SIPART PS100
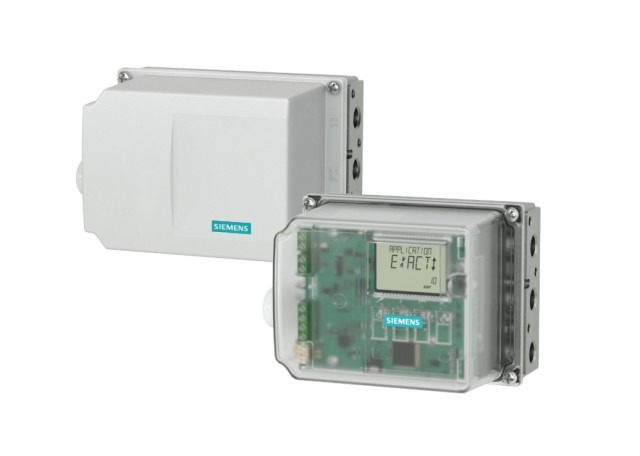
Positioner SIPART PS100
One that masters the essential
The SIPART PS100 is a compact and reliable valve positioner. Its ease and speed of initialization make it a winner for valve manufacturers, the chemical industry, the energy sector, and many other fields. The SIPART PS100 is available in two enclosure versions: aluminum or polycarbonate cover. With retrofittable Bluetooth functionality, it offers many other advantages.
SIPART PS100 positioner with polycarbonate lid and inspection window
SIPART PS100 electropneumatic positioner in aluminum enclosure without inspection window
The SIPART PS100 electropneumatic positioner is used to control the process valve or damper position of pneumatic linear or part-turn actuators. The SIPART PS100 electropneumatic positioners control the process valve according to the setpoint value.

Benefits
The SIPART PS100 positioners offer the following advantages:
- Fast commissioning at the push of a button
- Simple operation via the display and four buttons
- Display symbols according to NAMUR NE 107
- Negligible air consumption in stationary operation
- Setting the application profile based on predefined selection options, e.g. tight-closing valve, open/close valve, small valve
- Fast response in end positions ensures short positioning times and tight valves
- Insensitive to vibrations and steam hammer
- Leakage compensation ensures a constant actual value and protects the actuator
- Only one device version for linear and part-turn actuators
- Consistent parameter assignment with HART communication
- Safe use in hazardous areas
Application
The SIPART PS100 positioner is used, for example, in the following industries:
- Valve manufacturing
- Chemical industry
- Power stations
- Paper and glass
- Water and wastewater
- Food and pharmaceuticals
The SIPART PS100 positioner can be used with pneumatic actuators and an analog input (AI), 4 to 20 mA.

Design
The SIPART PS100 positioner comprises the following components:
- Enclosure (base plate with lid)
- Electronics
- Wear-free, contact-free position detection
- Pneumatic block
The pneumatic block is located in the enclosure, the pneumatic connections for the inlet air and the actuating pressure on the right-hand side of the enclosure. The electrical connections are located on the left-hand side of the enclosure.
The SIPART PS100 positioner is fitted to the relevant pneumatic linear or part-turn actuator using an appropriate mounting kit. The positioner shaft is located on the underside of the base plate. The positioner shaft is connected to the spindle of the linear actuator or the actuator shaft of the part-turn actuator using the mounting kit.
The electronics are available with the following options:
- Analog output (AO) 4 to 20 mA
The current position of the valve is converted into a 4 to 20 mA signal. - Digital input and digital output (DI and DQ)
- Position limit monitoring.
- Output of an alarm in the event of a control deviation or a device fault.
- Approach of a defined process valve position, disabling of keys, blocking of valve process valve by means of digital input.
- HART communication on parameter assignment and information on the device status
---------------------------------------------------------------------------------------------
Function
Local operation is performed using the built-in display and the four buttons. It enables, for example:
- Starting automatic commissioning with the press of a button
- Configuring the device
- Switching between the operating modes:
- AUTO: The positioner controls the valve according to the analog input (AI) 4 to 20 mA
- MANUAL: Valve movement with the middle keys
A hallmark of the SIPART PS100 is its own extremely low consumption of air. Compressed air is only required to move the valve. In the controlled state, consumption of air is negligible.
Technical specifications
Input | |
Analog input (AI), terminals 6 and 7 | |
| 4 ... 20 mA |
| 3.8 mA |
| 6.5 V (corresponds to 325 Ω at 20 mA) |
| ± 40 mA |
| HART 7 |
Digital input (DI), terminals 9 and 10 | |
| Electrically connected to analog input Galvanically isolated from the outputs |
| > 300 kΩ |
| < 3 kΩ |
| Suitable only for floating contact; max. contact load < 20 μA, 3 V |
Output | |
Analog output (AO), terminals 61 and 62 | |
| 2-wire connection |
| 4 ... 20 mA |
| < 3.6 mA |
| 12 ... 30 V |
| ≤ (UH [V] - 12 V)/IO [mA] |
| 0.05% |
| ± 0.3% |
| ± 0.1%/10K |
| ± 0.5% |
| Galvanically isolated from the other electrical inputs and outputs |
Digital output (DQ), terminals 31 and 32 | |
| 35 V |
| To be limited to 50 mA |
|
|
| I < 60 µA |
Operating conditions | |
Ambient conditions for operation according to IEC 60068‑2 | For indoor and outdoor use |
Ambient temperature | |
| ‑20 ... +80 °C (‑4 ... +176 °F) |
| 0 ... 100% |
Pollution degree according to IEC 61010-1 | 2 |
Overvoltage category according to IEC 61010‑1 | II |
Degree of protection of enclosure | |
| IP66 |
| Type 4X |
Corrosion protection according to EN ISO 9227:2012 and EN ISO 12944:1999 |
|
| C5‑M medium durability |
| C5‑M medium durability |
Vibration resistance | |
| 3.5 mm (0.14"), 2 ... 27 Hz, 98.1 m/s² (321.84 ft/s²), |
| 150 m/s² (492 ft/s²), 6 ms, |
| 10 ... 200 Hz; 200 ... 500 Hz; |
Pneumatic data | |
Pneumatic operating medium | Compressed air, carbon dioxide (CO2), nitrogen (N2), noble gases |
| 1.4 ... 7 bar (20.3 ... 101.5 psi) |
Air quality according to ISO 8573‑1 |
|
| Class 3 |
| Class 3 (min. 20 K (36 °F) below ambient temperature) |
| Class 3 |
Flow rate | |
|
|
| 7.1 Nm³/h (31.3 USgpm) |
| 9.8 Nm³/h (43.1 USgpm) |
|
|
| 13.7 Nm³/h (60.3 USgpm) |
| 19.2 Nm³/h (84.5 USgpm) |
Leakage actuator chamber (positioner portion) | < 6 · 10-4 Nm³/h (0.0026 USgpm) |
Consumption at operating medium in the controlled state | < 3.6 · 10-2 Nm³/h (0.158 USgpm) |
Sound pressure | LAeq < 75 dB LAmax < 80 dB |
Structural design | |
Supported actuator types | |
| 10 ... 130 mm (0.39 ... 5.12") |
| 10 ... 100° |
Weight, positioner without accessories | Approx. 1.0 kg (2.20 lb) |
Material | |
|
|
| Aluminum |
| Aluminum, anodized or stainless steel 316 |
|
|
Torques | |
| 1.5 Nm (1.1 ft lb) |
| 5 Nm (3.7 ft lb) |
| 12 Nm (8.9 ft lb) |
| 15 Nm (11.1 ft lb) |
|
|
| 12 Nm (8.9 ft lb) |
| 6 Nm (4.4 ft lb) |
| 4 Nm (3 ft lb) |
| 6 Nm (4.4 ft lb) |
| 15 Nm (11.1 ft lb) |
IMPORTANT: To avoid damage to the device, the NPT adapter must be held in place while the NPT gland is screwed into the NPT adapter. | 68 Nm (50 ft lb) |
| 2.5 Nm (1.8 ft lb) |
| 4 Nm (3 ft lb) |
| 6 Nm (4.4 ft lb) |
Pressure gauge | |
|
|
| IP31 |
| IP44 |
| IP54 |
Connections, electrical | |
| 2.5 mm2 AWG30‑14 |
| M20x1.5 or ½-14 NPT with NPT adapter |
Connections, pneumatic | G¼ or ¼-18 NPT |
Controller | |
Controller unit | |
| Adaptive |
| |
| ± 0.1 ... 3%, plus hysteresis (half of the deadband, but at least 0.2%) |
| Always active |
Analog input (AI), terminals 6 and 7 | |
| 50 ms |
| 0.05% |
Position detection | |
| 10 ms |
| 0.1% |
| 0.1%/10 K (0.1%/18 °F) |
Explosion protection | You can find details on explosion protection in the operating instructions and the explosion protection certificates: |